The theme of our two Cargo manipulation groups for the past two weeks has been "EVERYTHING IS CHANGING!"
This has been said at least once every other day about both our intake and the mechanism that wills store it and spit it out in to the rocket and cargo ship.
We have posted it about some of these changes from the our original concept of an extending intake that stayed down on the frame.
To a lower pivoting intake that mounts on the side of the cargo mechanism that is on the elevator.
We have built complicated contraptions like this one to try to test out concepts and prove the functionality of certain designs.

We made some crude hacks to see exactly what really works to try to force this ball into the center of the robot.

Over the past few days we have gone back to reevaluate some of our assumptions. Phrases like "What if they were both bottom rollers?", "The only thing changing is gravity". "This is the same really complicated sketch we have been looking at for 2 weeks, I just remade it and added colors.", "Who's spring is this?", "Everything is Changing!", and "What if we just flipped it all upside down?" have all been said and have been pretty important to the design process.
This is the sketch in question

Most of the robot gets designed in 2D like this before moving to 3D for the prototyping. This morning that was all we had after a lot of discussion last night about the changes and yes "flipping everything upside down". After about 2 hours of really fast CAD this afternoon we had a plan to build this.

This lets us put the prototype on the floor at the height that it will actually be on the robot when in this tipped down position.
It took another 4-5 hours to get it built and fully functional. That included laser cutting the panels, getting the rubber on too the polycarbonate tubing, pressing in tube connector nuts, and more.


We powered it using out prototype electrical board and our test pneumatics system that now uses our portable 60v Dewalt Compressor. The electrical board runs each motor off of a 20A breaker which is very useful because we did stall them a few times but the breakers did their job and prevented the motors from overheating.


Here it is in action.
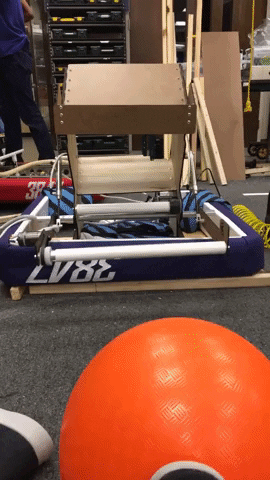
The roller system we are using is new to us this year. We have been trying to avoid having hex shafts go through bearings as much as possible because those systems always seem hard to maintain when you need to remove or add something.
Our roller system this year uses a 7/8" dead axle shaft with a 1.25" OD polycarbonate tube around it. The polycarbonate tube is running on two needle bearings and it's driven by a 3d printed pulley that has an integrated clamp to grip the tube. This setup lets us install and remove the roller with only two bolts going into the tube connector nuts pressed into the ends of the 7/8" shaft.

This version of the intake still has a lot of testing to do, and it's very possible that everything may change again but we made a lot of progress today.
Painting our practice field
The past few days we have also been working on finishing up our practice space and adding a dash of color to the elements.


- Spectrum